Expanding or upgrading operations in the food processing industry presents a critical decision for many companies. One of the central dilemmas they face is whether to repurpose an existing facility (brownfield) or start fresh with a clean slate (greenfield). This article explores the nuances of these options, shedding light on the pros and cons of each, while keeping in mind the unique considerations of Australian business leaders.
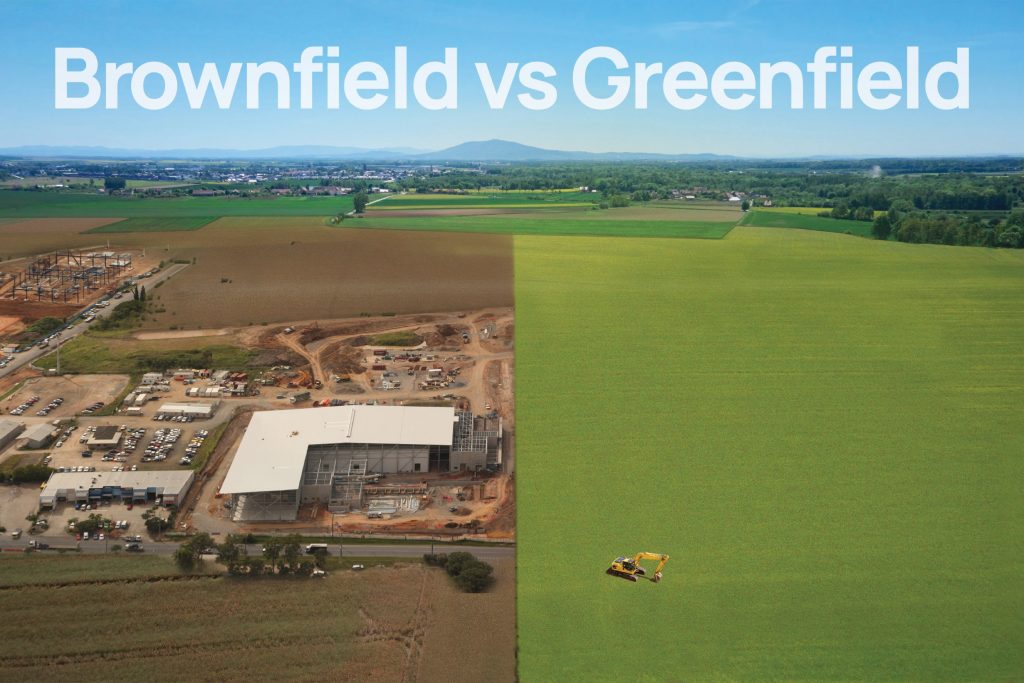
The pros and cons of brownfield vs greenfield projects
Defining Brownfield and Greenfield Sites
To start, let’s clarify the terms: a brownfield site typically refers to a parcel of land with existing buildings and structures which may be currently operating, whereas a greenfield site can be an entirely undeveloped parcel or a portion of land yet to be developed.
The Brownfield Advantage
- Time Efficiency: Brownfield projects can offer a time-saving advantage. Leveraging existing infrastructure may avoid the need for lengthy development or environmental approvals. This expedites the project, leading to quicker possession for manufacturing businesses, translating into faster income generation from the new facility.
- Geographic Benefits: Brownfield locations can also boast geographic advantages, including inner-city accessibility if proximity is crucial to your business and your workforce.
The Greenfield Edge
- Purpose-Built Development: The primary allure of greenfield projects lies in the ability to create a purpose-built facility. This reduces the need for compromises, as you’re not constrained by existing site conditions and structures. The blank sheet of paper the design process starts with offers limitless options on how you approach the project when compared to a brownfield site.
- Location Opportunities: Greenfield sites may enjoy location benefits, such as proximity to freeways and less congestion compared to inner-city locales that have gradually become more crowded over time. Furthermore, they may be situated in new development areas, presenting a modern and appealing image compared to older industrial zones.
Considering Costs and Timelines
While cost is a crucial factor, it’s not always the primary consideration. We all know the old adage that time is money – the faster your facility is up and running the sooner it’s working for you. This means that achieving early project completion can take precedence. Brownfield projects can excel in delivering early because you’re not starting from scratch, but it’s essential to note that costs can escalate when factoring in the retained value of an existing brownfield site.
Case Study: Adapting an Existing Warehouse
For instance, imagine a food manufacturer planning to transform an existing warehouse into a hygienic and temperature-controlled environment. The necessary upgrades may encompass a multitude of tasks, such as demolishing concrete floors, laying new slabs for drainage, reinforcing the roof structure, and reconfiguring internal building columns.
To make an informed decision you must assess the compromises being made to adapt the existing infrastructure. Consider the value retained from the brownfield site against the high-cost risks of alterations, including structural adequacy, compliance with new standards, and potential site contamination, among others.
Complexities in Brownfield Operating Sites
When dealing with an operating brownfield site where changes must occur while maintaining operations, the project’s dynamics change significantly. Staging the project can add time and cost. A potential solution is designating a vacant portion of the site as “greenfield.” Here, you can construct the expansion, relocate a portion of the operation, and then make necessary changes to the original brownfield building. This approach minimizes disruptions to production flows and hygiene, ultimately delivering better value for capital investment.
It is worth noting that delivery of a construction project, machine installation and commissioning on an active operating site is a complex undertaking and requires specialist skills and planning to ensure safety to those delivering the project and to the operational staff. It is also critical that the project is planned around operation to ensure minimal if any disruption to ongoing production.
Seeking Professional Guidance
Perhaps the most critical aspect to consider is seeking professional advice. Engage experts to conduct due diligence on your options. This typically involves experts in town planning, surveying, architecture, engineering (both structural and services), and compliance certification. While you can choose to consult some or all of these experts, it’s essential to maintain a holistic approach.
Wiley: Your Holistic Partner for Food Industry Challenges
Wiley brings a wealth of experience to the table, specializing in the unique challenges of the food industry. When making critical decisions about brownfield or greenfield projects, our team of professionals can provide you with reliable advice tailored to your specific needs.
Conclusion
In the end, the choice between brownfield and greenfield projects in the food processing industry hinges on multiple factors, with cost and time being only part of the equation. Australian business leaders should carefully evaluate their goals, existing infrastructure, and the potential for future growth. By seeking professional advice and taking a holistic approach, you can ensure that your expansion or upgrade project aligns with your long-term business objectives and sets you on a path to success in Australia’s thriving food processing sector.